コラム
Column
2022.07.11
「工場 業務改善」は3ム主義「ムダ・ムラ・ムリ」に始まる
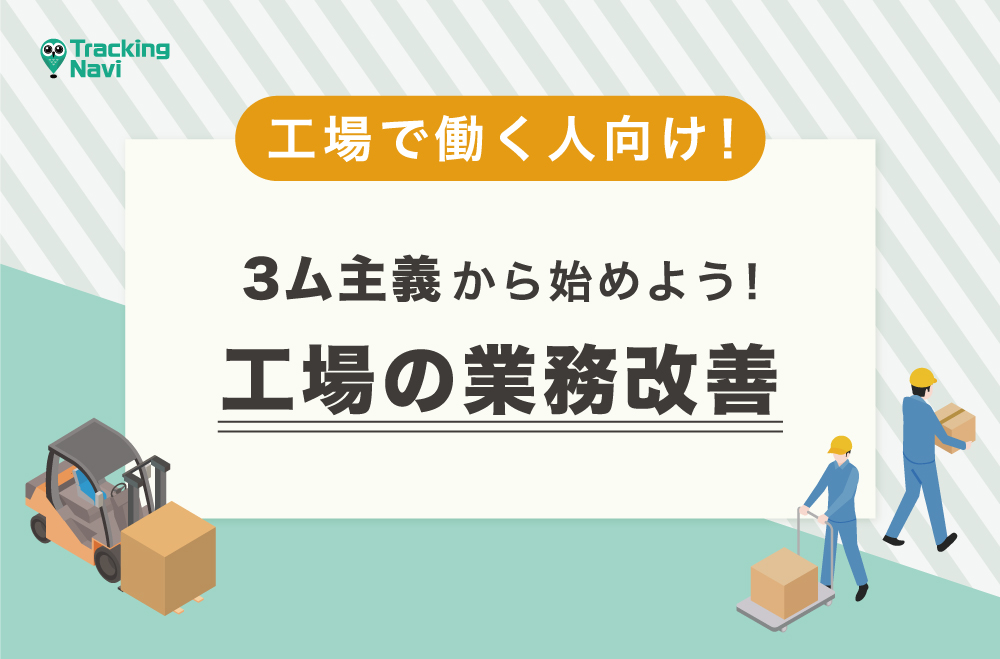
「3ム主義」とは、「ムダ・ムラ・ムリ」を排除して生産効率を高めようとすることです。 「ムダ・ムラ・ムリ」は「効率を落とす3要素」とも言えるものです。 また、このスローガンの裏には「発想の転換」を迫る意味合いが強くあります。
現在では、ITを始めとして業務効率を上げるための様々なテクノロジーがあります。
装置の状況、モノの動き、人の動きなどをデータとして蓄積することもできるようになってきました。
しかし、データの意味を読み解く時、平均や標準偏差などの学問的解釈にこだわって、実態を掴めていないことがあります。
データが収集された条件や背景などを広く俯瞰して眺め、データから実際の動きを掴むことができなければ、生産管理、生産技術では大きな間違いを起こします。
目次
工数のばらつきはどうして起きるのか?
生産管理において、データに現実を無理に合わせようとする人がいます。
現場で「工数のばらつきはどうして起きるのか?」と考え込んで、「工数を安定させるにはどうすればよいのか?」と考えるのです。
間違いではありませんが、現実には「手作業やロット生産」の工程が多く組み合わされているため、細かい待ち時間が積み重なって、工数のばらつきが生じてしまいます。
人間は頑張ると20%程度まではすぐに効率が上がる
人間は、短期間では20%程度なら頑張るだけで効率を上げてしまいます。
そのため、工場に限らず業務改善する場合の目標は、少なくとも30%アップ、出来れば50%以上の目標を掲げます。
すると人は「これまでの延長線上にはない発想の転換」を目指すようになります。
生産性向上のカギは人間の持つ柔軟性
業務改善により50%を超えるような高い生産性向上を目指すには、設計から製品の加工工程に至る業務プロセス自体を変える必要があります。
例えば「デジタル屋台」の導入や、現在、世界中の自動車企業で行われている「プラットフォームの共通化」などです。
しかし、業務プロセスの変革を「受注・生産・販売・サービス」まで全体に浸透させるには、サプライチェーンまで含めて考える必要があるため容易ではありません。
いくらデータ化をすすめても、そのデータを読み解き意思決定するのは人間です。
結局、工場の業務改善のカギは「人間の持つ柔軟性」なのです。
「業務改善」を行う手掛かりは「3ム主義」にある
業務改善を始めるとき、何らかの手がかりが必要です。そこでよく利用されるのが、「3ム主義」です。 3つのムとは「ムダ・ムラ・ムリ」を取り除くことです。
「ムダ・ムラ・ムリ」を発見するには、まず現状を把握する必要があります。
現状の把握で最も基本的かつ重要なことは実際の現場を観察することです。
一方で、「ムダ・ムラ・ムリ」はどこに潜んでいるか分かりません。
生産量、対象製品、工程、作業者・・・こういった要素の特定の組み合わせでのみ発生する「ムダ・ムラ・ムリ」がありますが、全てを観察することはできません。
そこで、動線分析システムや可視化ツールを使って、効率よく人や物の動きの全体像を把握し、観察すべきポイントを絞る必要があります。
動線の可視化で「ムダ」な運搬を発見する
動線分析システムでは、工場や倉庫のレイアウト上に、作業者が移動した軌跡を表示することができます。 このような「動線の可視化」を行うことで、いままで気づけていなかった「ムダ」を発見できます。
動線を可視化した時、同一工程の作業中に頻繁に移動が発生している、フォークリフトなどの車両と人の動線が交差している、といったことが見られると、ムダが生じていたり、時には危険な状況が潜んでいたりする可能性もあります。
“運搬のムダ”ということが言われますが、作業者の移動、つまり“運搬”は付加価値を生み出さない作業です。
また、移動を繰り返すことで、キズや打痕などの不良を生んでしまうこともありますので、ムダな運搬は極力排除する必要があります。
「ムラ」を無くす「平準化」のすすめ、平準化の効果とは?
「ムラ」が「ムダ」を生み出す
先ほどあげた作業者の動線でも、「ムラ」に着目して業務改善を進めることができます。
例えば、製品、作業工程が同じであるのに、時期や時間帯、作業者によって動線がまちまち、つまり動線にムラがある場合、何らかの条件が安定していないことを示しています。
作業者によってムラがある場合、作業指示書の記述があいまいである、あるいは教育が行き届いていないのかもしれません。
こういった事象が発生している場合、以下のステップで改善を進めると良いでしょう。
- 動線で作業者が移動した軌跡を可視化する
- 動線や作業時間を分析し、特異点(他と異なっている点)を発見する
- 特異点が発生している現場を観察し、原因を特定する
- 原因を解消できるような平準化を進める(すなわち、ムラを排除する)
物を動かすべきか?人が動くべきか?重量で決まる?
物の動線、人の動線をたどる時、作業の本質を知っておく必要があります。
生産技術において、特に「レイアウト」「作業手順」を考える時、多くの製造業では「物を動かすべき」との固定概念があります。
しかし、必ずしも物を動かすことで作業が楽になるとは限らないのです。
取り扱う物によっては、「物を動かすべきか?人が動くべきか?は重量で決まる」とみてよいはずです。
造船ではモジュ―ル生産になっても、物を動かしながら作業をすることは基本的に非効率です。作業者が作業場所に動いて作業するしかない場合が大半です。
こうした職場では作業者の動線を効率化することが、業務全体の効率化にとって非常に効果的です。
一方、事務機のコピー機を組み立てる時は、人は動かず物を動かすことで「楽に、早く、確実」に作業が出来る場合が多いです。
自動車の組み立てでは、全体はベルトコンベアで物を動かすことにしていても、細部では人が動いて作業することが多いでしょう。
フォークリフトやクレーンの他、最近ではAGVやRGVなどの無人搬送車も利用が進んできました。
多くのものを一度に運べるため、上手く使いこなせれば大幅に効率を上げることができます。
しかしながら、フォークリフトやクレーンで物を動かすには免許が必要で、技術を持った作業者や車両の数も限られており、当然コストもかかります。
その為、導入にあたっては、最も効率が上がる適用場所がどこかを事前に検証しておく必要がありますが、ここでも「取り扱う物の重量」を視点の一つとして考えるべきでしょう。
「ムリ」を無くす。例えば、作業姿勢に「ムリ」はないか?
「ムリ」の中では、作業量が多すぎることが一番目に付きます。
しかしその原因は、「作業姿勢」が最適でないために無理な動作や不要な動作が多くなり、結果として作業量が増えてしまっているという可能性もあります。
このような「ムリ」が生じているかどうかを発見するには、作業の観察と分析が有効ですが、全工程の全ての作業者の作業を観察・分析するには膨大な時間がかかります。
効率よく分析を進めるには、IT技術を上手く活用し、網羅的に集めたデータから観察すべき作業を見極めることがポイントです。
ムダ発見後のカイゼン
ムダが生じている箇所や原因が発見されたあと、それを改善しようとする時は、最適な作業工程を見つけ出し、工程を変更するために必要な製造技術を開発しなければなりません。
このとき、中間在庫を少なくする方向で考えると、正解が見つけやすいです。つまり、「工程を結合させてしまう」ことを検討します。
例えば、最近では3Dプリンタの登場で、複雑な形状の部品を一体で作れるようになり、組み立ての必要が激減して、工程が削減できるようになってきています。
また、多品種生産への対応や製造リードタイムの短縮が求められる場合は、「ライン生産方式」から「セル生産方式(屋台)」に切り替えることを検討します。
「セル生産方式」に切り替えて工程を結合することで生産性が柔軟になり、中間在庫が削減されます。中間在庫が無くなるということは、中間在庫の運搬作業も、置き場所も不要となるのです。
まとめ:「工場 業務改善」は3ム主義「ムダ・ムラ・ムリ」に始まる
工場の業務改善と言っても、指し示す範囲はかなり広くなっています。
的確に問題点である「ムダ・ムラ・ムリ」を探し出すには、「問題意識」つまり何がムダかを常に考えていることが必要になります。
「初めに問題意識あり」が重要です。そのきっかけを示してくれるのが3ム主義「ムダ・ムラ・ムリ」なのです。
お電話でのお問い合わせ
【東京】03-3257-1141
【大阪】06-6442-1329
受付時間:
平日9:00 - 17:00
(土日祝日、年末年始を除く)