コラム
Column
2022.07.11
「工場の見える化」でTOCを実践する
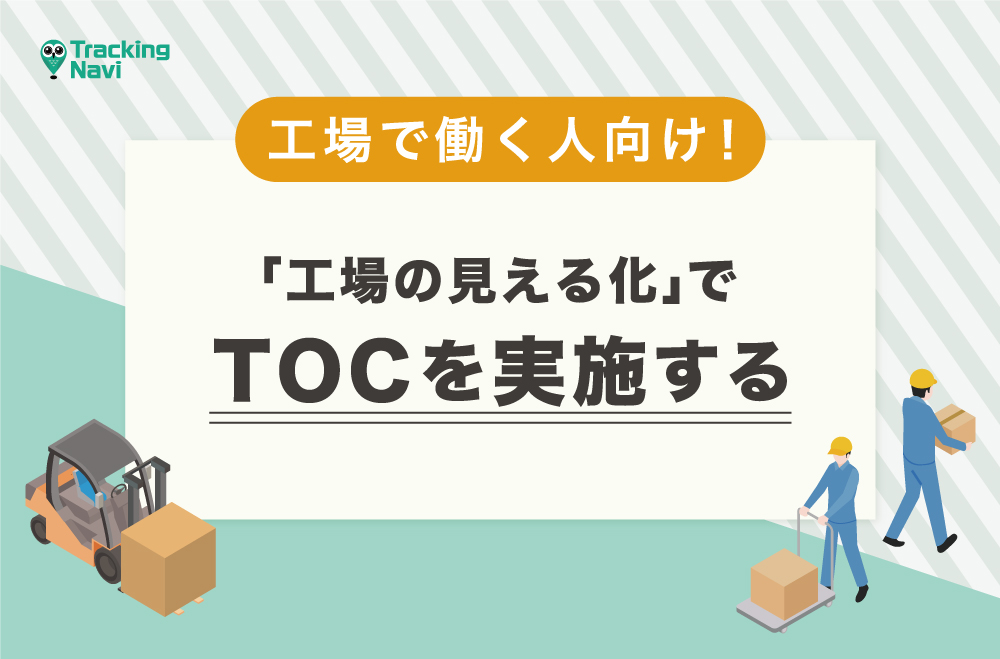
製造業に従事される方であれば、「TOC」という言葉を聞かれたことがある方も多いと思います。
TOC(Theory of Constraints)理論は、イスラエルの物理学者であるエリヤフ・ゴールドラット博士が開発した、仕事の効率をあげるためのマネージメント理論です。
「トヨタ生産方式」の考え方も取り入れているということですが、製造や物流のみならず、営業部門やIT部門などでも活用されています。
TOC理論に基づいて改善を進めるにあたっては、まず現状を把握することが重要です。
本コラムでは、TOC理論の基本的な考え方と「見える化」の必要性について解説します。
目次
工場の生産性向上とは?
工場で製品を生産する目的は、生産した製品を顧客に販売し、利益を得ることです。
このとき、生産を行う際に投入するリソース(労働力、設備、原材料)が少なければ少ないほど、「生産性が高い」ということになります。
中間在庫が多いと管理のための無駄なコストが発生してしまいますので、不要な中間在庫はなるべく少なくする必要があります。
また、投入資金を早く回収する、つまり、販売までのリードタイムを短縮することも併せて考える必要があります。
従って、工場の生産性向上とは、個々の工程や機械設備の生産量をあげることではなく、顧客からの注文が入ってから販売できる状態にするまでの全体の速度、すなわちスループットをあげるということになります。
TOC理論では、全ての工程のうちで最も処理能力が低い工程=「ボトルネック(ビンの首)」を解消することで全体のスループットが上がるとしています。
「ボトルネック」とはその処理能力が、投入される仕事量と同じかそれ以下のリソースのことです。
その反対が「非ボトルネック」で、投入される仕事量より処理能力が大きいリソースのことです。
非ボトルネック工程の効率がいくらあがっても、ボトルネック工程の効率が向上しなければ、中間在庫がふえるだけです。
工場全体のスループットを上げるには、ボトルネック工程のフローにあわせて、資材投入、非ボトルネック工程の稼働を調整する必要があります。
ボトルネック解消の5ステップ
ボトルネックを解消するには、以下の各ステップを順番に進めていきます。
ボトルネックとなっている工程を見つける
ボトルネック工程を見つけるには、まず工場の現場をよく観察する必要があります。
・作業が停滞している工程、仕掛品が積みあがっている工程がないか。
・足りない部品がよく発生する工程の前工程がボトルネックとなっていないか。
・稼働率が高い工程がないか。
・作業時間が最も長い工程はどこか。
・トラブルが多く発生している工程はどこか。
最新の設備が入っていてもボトルネックとなっている可能性はあります。また、時間帯や季節による波動があるため、部分的な観察ではボトルネックが発見できない可能性もあります。 そのため、人による観察とともに、データに基づいた網羅的な把握も必要です。 IoT等のITを活用することで、全ての時間帯、行程の稼働状況や作業時間を継続的に把握することができます。
ボトルネックの工程をフル稼働させるにはどうするかを考える
ボトルネックとなっている工程が発見できたら、ボトルネック工程と非ボトルネック工程をわけた上で、ボトルネックとなっている工程をフル稼働させるにはどうするかを検討します。
ボトルネックの時間のムダをなくすこと、ムダな作業を行っていないかなどを考えます。
・従業員の休憩時間などで機械が停止している時間がないか。
・工程の段取りを改善することで工程時間を減らせないか。
・ボトルネック工程に必要な部材は必要最小限のものが常に置いてあるか。
機械や人員を導入し、ボトルネック工程の生産量を上げるのが分かりやすい対策ですが、機械や人員の導入にはコストや時間がかかりますので、 まずは現状の工夫で改善できることがないかを考えましょう。
ボトルネック工程をフル稼働させるために全体の工程を再設計する
上述のボトルネック工程をフル稼働させるため、工場全体のプロセスを見直します。
(前後の工程だけでなく工場全体でモノや人がどのように流れているかを把握し、プロセスを見直します。)
・ボトルネック工程の前に品質検査を行い、欠陥部品がボトルネック工程に流れないようにする。
・ボトルネック工程の前工程の加工の工夫で、ボトルネック工程の処理時間を短縮する。
・従業員の休憩時間を工夫し、機械がとまらないようにする。
・スペアパーツなど、オーダーになくすぐに売れる見込みのない部品を作らないようにする。
・ボトルネック工程で必須となる仕掛品が他の工程で優先的に処理されるように目印をつける。
ボトルネック工程の能力を高める
工場全体のプロセスを見直したのちに、機械設備の増強や人員増強でボトルネック工程の能力をあげることを検討します。
新たなボトルネックを発見する。(ステップ1に戻る。)
当初にボトルネックとなっていた工程の処理能力があがったことで、新たに異なる箇所がボトルネックとなってくることがあります。
また、環境が変化することで、ボトルネックも絶えず変化しています。
・市場ニーズの変化による製造製品の種類/量の変化
・供給される材料の変化
・世代交代や外国人労働者の採用などによる作業者の変化
こういった変化に対応するため、ボトルネックの発見と改善は継続的に行う必要があります。
ボトルネック工程をフル稼働させるには、非ボトルネック工程にも“あそび”が必要
特に人が行う工程が含まれている場合、「統計的変動」と「依存的事象」が組み合わさって、思いもよらない遅延を招くことがあります。
例えば、A→B 2つの工程があり、1時間あたりの処理量がそれぞれ以下とします。
A工程 25個 → B工程 25個
各工程の処理量がばらつかず、正確に25個処理できれば、A工程へ材料を投入してから2時間後には25個の製品が完成するはずです。 ところが、実際の各工程の処理量には変動が生じます。 これは、処理量が25個といったとき、実際には“平均25個”や“正常稼働時は25個”ということであり、実際の処理量は22個や27個などバラツキ=統計的変動が発生するためです。
また、作業工程には依存関係があるため、後工程で処理できる最大個数は前工程の処理数以下になります。
B工程の処理量が最大25だとしても、A工程の処理量が21個なら、B工程の処理量も21個になってしまいます。
A工程 21個 → B工程 21個
ここで、A工程の作業者が遅れを取り戻そうと、次の1時間に29個を処理したとしても、B工程の処理量に遊びがなく最大25個だった場合、結果として完成品の量は増えません。
【1回目】A工程 21個 → B工程 21個
【2回目】A工程 29個 → B工程 25個
この例では、2回の合計で50個の完成品を期待していましたが、バラツキと依存の影響で、46個しか完成しなかったということになります。
こういったバラツキに対応するためには、処理能力に余裕を持っておく必要があります。
効率よくボトルネックの解消を進めるには?
「ボトルネック解消の5ステップ」に記載しましたが、時間帯や季節による波動があるため、人手による部分的な観察だけではボトルネックが発見できない可能性があります。
また、工場を取り巻く環境(顧客ニーズ、作業者、仕入れ先・・・)の変化によって、ボトルネックそのものも絶えず変化しています。
このように、ボトルネックが見つけにくくなっている昨今においては、人による観察とともに、データに基づいた網羅的な状況把握が必須となってきています。
以下の手順ですすめることで、漏れなく、また効率よくボトルネックの解消を行うことができます。
1.IoT等のITを活用し、工場全体の状況を「データ化」する。
・装置や部材の動きだけでなく、作業者の動きも可視化
・全ての時間帯、作業工程の稼働状況や作業時間を継続的に把握
2.収集したデータを「見える化」し、ボトルネックの見当をつける。
・差異(作業者、時間帯、製品による差異)
・作業時間
・作業者が運搬に要した時間、移動距離、手待ち時間
3.見当をつけた箇所を実際に観察する。
・現場に足を運び、実際に観察
まとめ:「工場の見える化」でTOCを実践する
工場で製品を生産する目的は、顧客からの注文に基づいて生産した製品を販売し、利益を得ることです。
工場の生産性を上げるとは、顧客からの注文が入ってから販売できる状態にするまでの全体の速度、すなわちスループットをあげるということです。
スループットを上げるには、全ての工程のうちで最も処理能力が低い工程=「ボトルネック(ビンの首)」を解消する必要があります。
ボトルネックを解消するには、まずボトルネックがどこかを発見する必要があります。その為には、現場観察に加えて、IoTの活用で設備や作業者の稼働状況をデータとして蓄積・分析し、効率よく進めることがポイントです。
お電話でのお問い合わせ
【東京】03-3257-1141
【大阪】06-6442-1329
受付時間:
平日9:00 - 17:00
(土日祝日、年末年始を除く)