コラム
Column
2022.09.02
工場経営に必須の工数管理。今のやり方で大丈夫?
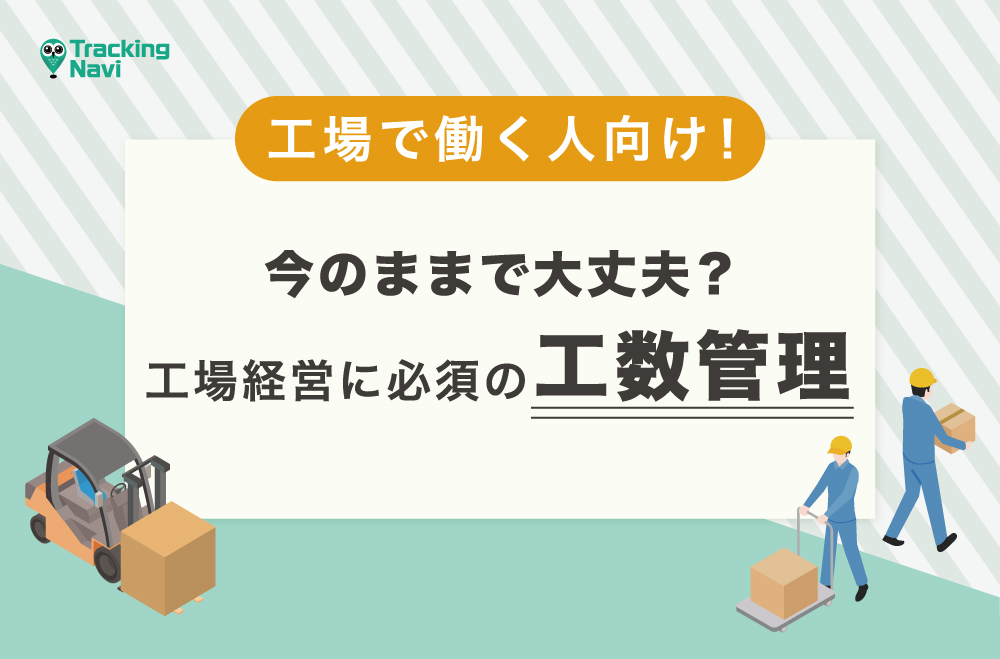
皆様の工場でも、なんらかの形で作業の工数管理を行なっていることと思います。
しかしながら、現在行っている工数管理は、ビジネスを発展させることを目的と考えた時、管理対象や精度において十分と言えるでしょうか。
本コラムでは、工数管理を行う必要性について改めて整理し、現状の工数管理の課題と工数管理を成功させるポイントを解説します。
目次
工数管理の必要性
企業の存在意義は、社会や顧客に対して価値を提供し、その対価としての利益をあげることですが、その利益を確保するために、工数管理はなくてはならないものです。
工数管理は業務改善の第一歩
競合や顧客ニーズなど、企業を取り巻く環境は絶えず変化しており、利益を確保し続けるには継続的な業務改善が必要です。
業務改善においては、作業工程の工数を把握・分析し、無駄や非効率な部分を可視化することが必要です。その結果、優先して改善すべき部分がわかります。また、改善が期待したとおりの効果を生んでいるか、計測・評価することができます。
精度の低い工数管理は誤った意思決定の原因
事業戦略上の意思決定を行うには、正確な原価の把握が欠かせません。
原価が不正確だと、その製品がどの程度利益を上げているか、(あるいは損失が発生しているか)という情報も誤ったものになり、誤った意思決定を招いてしまいます。
“作れば作るほど、実は赤字になっていた“ということを避けるには、正確な工数管理が欠かせません。また、製品ライフサイクルの短い製品では、減産や製造切替の判断を迅速に行うため、日次や週次などより高い頻度での情報の更新が求められます。
工数見える化は自律的改善のポイント
工数実績を作業者自身に対して「見える化」することで、作業者のモチベーションアップに繋げることもできます。
テレビでもよく取り上げられていますが、最も簡単なダイエット方法は、「体重計で体重を計りグラフに記録していく」ことだそうです。体重をグラフに記録する習慣をつけると、右肩下がりのグラフを見ることがいつしか食事以上の快楽になって、やせられるというメカニズムだそうです。
つまり「見える化」することが“改善”に繋がっているというわけです。
工数管理の手法と課題
このように、さまざまな観点から企業活動に必須と言える工数管理ですが、現状の手法では課題も多く見られます。
従来の方式としては「日報、作業実績報告書や指示書に手書き」、「紙のタイムレコーダー」といったものがあります。
こういった方式では、以下のような問題があります。
・作業者自身による申告のため不正確な場合がある。
・工程単位の細かな工数の記録は、作業者の負担が大きいため、継続的な実施が困難である。
・紙での記録では、保管や情報の検索、集計が困難である。
・紙での記録では、電子化するために追加のコストがかかる。
最近の工数管理の手法
こういった問題を解決するため、「バーコード入力」、「NFC」といった作業者になるべく負担をかけず電子的に記録できる方式が出てきています。
特に「ビーコン」を利用した方式では、作業者の現在位置と滞在時間を記録することで、作業者の操作は一切不要で、自動的に作業時間の実績を記録することができます。
作業場所と作業内容が一対一に紐づけられている必要はありますが、作業者に負担をかけずに、日報やタイムレコーダーより遥かに正確で細かなデータを取得できるところが魅力です。
こういった工数管理が、製造業で発生する課題の解決に、どのように役立つのかを見ていきたいと思います。
大ロット生産による遅延解消
工場の生産現場では、種々の理由で「少量生産」になっていない工程が数多く存在します。 メーカーの組み立てラインであれば「多種少量生産」「混流生産」となってきていますが、サプライヤーでは、まだ多くの製造現場でロット生産となっています。それは、製造過程の途中に「混流生産」出来ない工程(例:焼き入れ、ボーリング、鋳造工程など)があるためです。
こうした工程では、少しの遅れがあって先に他部品の作業が始まってしまうと、先に加工が始まっている部品のロット全ての加工過程が終わるまで、待つことになります。 この時、一つの工程間のタイミングのずれは少しでも、工程全体でみると遅延が大きくなりますし、影響範囲がそのロット全体となるため、大幅にスケジュールが狂ってしまいます。
こういった待ち時間をなくすための一つの解決策は、少量ロット生産にすることです。 少量ロット生産にすることで混流生産が可能となり、後工程の待ち時間を短縮することができます。それには加工する部品ごとに行う「段取り」時間を最小にしなければなりません。 これを疎かにしたまま混流生産にした場合、段取り時間がかかり生産に大きなダメージを受けてしまいます。
自動車のボディ製作過程には大型プレスの工程があり、車種が違うなどすると、プレス金型を取り換えなければなりません。 ある工場では、この大きく重い金型の交換に4時間かかるため、後工程に大きな待ち時間を発生させていました。しかし「外段取り化」により内段取りの待ち時間を7分ほどに短縮することで、「混流生産」を実現することができました。
こうした「少量ロット化」や「段取り替え」の作業改善が実際に効率向上につながるかどうか、実際にラインを組み替える前に見積もりしておく必要があります。 現状の作業工程ごとの工数がデータとして記録されていると、分析や改善の見通しを容易に立てることができます。
持続可能な効率向上
人の行う作業は、短期間であれば「頑張る」ことで簡単に効率アップできてしまいます。
しかし、その高効率は、疲労のため長続きはしません。
短期間であれば効率を上げられることから、太鼓をたたき、叱咤して人を使おうとする組織も存在しますが、製造業でこのようなムリを続けると、「品質」に問題を起こしたり「事故」に結び付いたりします。
大事なのは、持続可能なペースで作業をしても効率が上がるように、作業環境やプロセスそのものを改善することです。
こういった改善に基づいた持続的な効率向上を行うには、まず現状の工数を常時かつ網羅的に計測する仕組みが必要です。
常時計測することで、効率の向上(または低下)が一時的なものか持続的なものかが把握できます。
また、網羅的に計測することで、特定の工程や人に固有の課題なのか、組織全体の課題なのかを判断できます。
次に、動線解析や現場の観察によりボトルネック工程を分析し、そこから「ムダ・ムラ・ムリ」を見つけ出し、作業環境やプロセスの改善を行っていきます。
こうすることで、「頑張ることで達成する効率アップ」から「日常業務」としての安定的な効率向上を行えるようにしていきます。
こういった現場の業務改善にもとづく効率向上には、作業者による自発的な「改善活動」が不可欠です。
人事制度や表彰制度、福利厚生設備などの支援の他、作業工数を作業者自身に「見える化」することによって、改善意欲を上げることも有効と考えられます。
機械の稼働率優先から全体スループットの向上へ
製造業では高価な工作機械を使う工程が少なからず存在し、設備投資効率向上のため、休止時間を作りたくない機械(工程)があります。 大事なことは、工場全体のスループットを上げることであり、特定の機械の稼働率を上げることではないのですが、高価な工作機械を購入してしまった手前、「機械の稼働率」中心の管理がなされていることも多くあります。
すると、その機械工程中心にスケジュールが組まれ、その機械工程の前で作業待ちの時間が頻発することになります。
少しでも前工程が狂うと、待ち時間が生じてスケジュールの変更が全工場に及んでしまうなど、大きな問題を生じる場合があります。
また、この調整は頻繁に必要で、また製造技術を理解している必要もあるため、工程管理者に任せっきりになっているということもあります。
こういった問題の解決には、特定の機械の稼働率だけでなく、その他の工程にも目を向ける必要があります。
ボトルネック工程を見つけ出し、その工程をフル稼働させるにはどうするかを検討します。ボトルネックを発見するには、人による観察とともに、データに基づいた網羅的な把握も必要です。
IoT等のITを活用することで、全ての時間帯、行程の稼働状況や作業時間を継続的に把握することができるようになります。
工数管理の切り札、「作業者位置情報」の把握
工数を把握するには、冒頭に記載した通りいくつかの方法があります。
しかしながら、工数管理を有効な改善につなげていくためには、作業工程別の精度の高い工数を把握し、「ばらつき」が生じているかどうかも含めて「見える化」する必要があります。
また、作業工数を把握することが作業者の負荷になり、業務効率を下げてしまっては本末転倒となってしまいますので、作業者の負荷にならない方式を採用する必要があります。
さらに、工数を記録した後、すぐに分析するためには、予めデジタルデータとして記録しておく必要があります。
整理しますと、改善につなげるための工数管理では、以下のポイントを押さえておく必要があるということになります。
・作業工程別に(分単位など)精度の高い工数を記録できること
・作業者に負荷がかからないこと
・デジタルデータとして記録できること
こういった要件を満たす工数管理の方式はいくつか考えられますが、比較的導入が容易なものとして、冒頭でも例にあげました「ビーコン」等による「作業者の位置情報」を利用する方式があります。
この方式では、作業者がスマートフォンやビーコンなどの機器を身に着けているだけで、自動的に作業時間の実績が記録されます。
作業者による操作は一切不要なため、作業者に余計な負担をかけることもありません。
デジタルデータとして記録されますので、保管や分析、「見える化」が行いやすくなります。
これまでは手作業による工数管理が中心で、記録が不正確で粒度が粗く、改善の分析にはあまり役に立たないものが多くありましました。
上記のポイントを押さえた方式を採用することで、改善に繋がる工数管理を行えるようになります。
まとめ:工数管理は企業に必要不可欠。でも今の方法で大丈夫ですか?
正確な工数管理は、「業務改善」や「原価管理」になくてはならないものです。
しかしながら、現状は作業者自身が手書きで記録することが多く、正確さや細かさにおいて、十分であるとは言えません。
不正確な工数管理では精度の低い改善しか行えません。また、改善の成果を測ることもできません。
不正確な工数管理では、事業戦略の意思決定に重大な誤りをもたらす可能性があります。
適切な工数管理を行うには、工数を把握する目的や作業者への負担を考慮し、記録した情報を分析することも踏まえ、最適な方式を選択する必要があります。
お電話でのお問い合わせ
【東京】03-3257-1141
【大阪】06-6442-1329
受付時間:
平日9:00 - 17:00
(土日祝日、年末年始を除く)