コラム
Column
2022.09.16
倉庫作業の業務改善で効率化を図ろう!
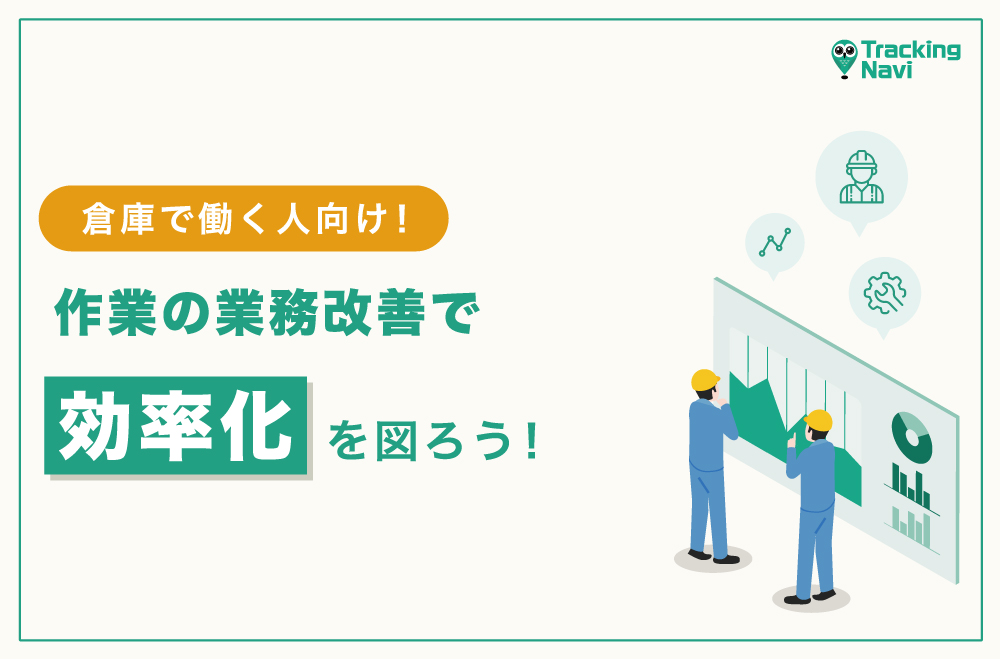
倉庫作業の効率化を図るのに頭を悩ませている担当者の方は少なくありません。納期の指定、積み荷の品質など、クライアントの要求はシビアになればこそ、緩むことはないでしょう。
こういったクライアントの要求に応えるため、倉庫作業の業務改善が必要になるのですが、現場の手作業だけで実施するには限界があります。ここでは倉庫作業の業務改善で効率化を図るために必要な現状把握、改善のポイント、システムの導入を解説していきます。
目次
倉庫作業の現状やムダを把握する
倉庫作業の業務改善を考える前に、まずは現状の把握が大切です。倉庫作業の現場に潜む問題や、作業効率や時間のムダがどれだけあるのか順に追っていきましょう。
整理整頓ができていない
整理整頓ができていない倉庫は、ただ散らかっていて見た目がよくないという表面的なことにとどまらず、常に作業上のムダを生んでいるという問題を抱えています。
この要因は、倉庫内で製品や荷物の場所が決まっていないことです。
根本的に3定(定位、定品、定量)ができていないと、入荷したものを空いているスペースへ適当に置いてしまい、出荷・運搬する時にはそれがどこに保管しているかわからずに探し回ってしまいがちです。
このような倉庫は見える化ができておらず、また作業者ごとにモノの配置も変わるため、余計に探す手間が増えてムダな時間が生じます。
作業者が次に何をしていいのか分からない(指示待ち)
作業者の手が空いているにも関わらず、次に何をしていいのか分からず指示待ちになっている状態があれば、待ち時間のムダが生じています。 だれが次に何を行うのかが明確になっていない場合、倉庫作業の責任者やリーダーが絶えず指示を出さなければ作業者の手が止まってしまいがちです。 このような指示待ちの状態が日常的になっているとすれば、その時間はムダといえます。
台車を探す時間がかかる
倉庫内には、製品や荷物の他に、運搬時に使用するツールが乱雑に置かれているケースもあります。例えば製品を台車で運ぼうとした時、その台車を探すことに時間がかかっていると、運搬作業のスタートに遅れが出ます。 こうした少しずつのロスが積み重なって、倉庫内で作業効率が低下します。
作業者によって実績がばらつく
倉庫作業者によって実績がばらついている場合、作業のやり方が統一されていない可能性があります。作業者が独自の方法で作業を進めているので、作業効率も悪くなり、かかる時間や成果にもムラが出てきます。
倉庫作業における業務改善のポイント
倉庫作業の現状と、どこにどれだけのムダが生じているかを把握した後は、それらを改善していかなくてはなりません。それぞれのムダを省いていくことが倉庫全体の業務改善にもつながります。倉庫作業の業務改善のポイントをみていきましょう。
どこに何がどれだけあるのかを見える化
倉庫にはさまざまな製品が保管され、日々入荷と出荷を繰り返して動き続けています。 倉庫作業者が忙しさに追われて、空いているスペースに荷物を適当に積んで、行き当たりばったりで物を探し回っていると、当然ながら作業効率は落ちますので時間のムダも生じます。
倉庫内のどこに何がどれだけあるのかを把握していれば、必要なものをすぐに見つけられるため、倉庫内の棚の列や段ごとに保管場所を指すロケーション(住所・番地)を定めます。 倉庫内の保管場所を見える化することで、だれが作業をしても一目でわかるような仕組み作りが大切です。
作業者のルートに運搬物やピッキングの製品を常に配置
作業者が手ぶらで歩いている状態が多い倉庫は、それだけムダな時間を生み出しているといえます。倉庫作業の業務改善には移動と作業とが常にセットとなるような仕組み作りが大切です。 そのためには棚や物の配置を見直し、作業者が移動するルートに運搬物やピッキングする製品を配置しておくことが効果的でしょう。
また、倉庫作業者によってそれぞれのやり方や勝手なルートで作業してしまわないよう、事前にどんな手順で作業するのかなど、作業前の確認や情報共有も忘れずに行いましょう。 ムダのない配置作りに加え、そのルートを確実に移動させることで倉庫全体の作業効率が上がります。
運搬用ツールの位置情報も把握
倉庫内のどこに何があるかという見える化には、製品だけではなく、作業に使用する道具にも当てはまります。 運搬用の台車やカートの位置を作業者全員で共有し把握しておくことで、そのツールを探す時間が短縮され、動きにムダがなくなります。
倉庫作業における業務改善の一貫として、製品と同じように、運搬用ツールについても定位置を決めておき、使用後は必ずこの場所に戻すという明確なルールを作っておきましょう。
作業者の移動回数や距離を減らす
倉庫内のレイアウトによって、作業者が一度通ってきたルートを引き返すことや遠回りしなければ運搬できないということもあります。 ムダがなく最短距離で移動ができるように、最適な運搬ルートを決めておかなくてはいけません。
倉庫内の棚のレイアウト変更し、運搬記録を付けて作業者の行動を把握することも必要になります。倉庫作業者の移動回数や距離が削減すれば、その分だけ作業効率の向上に直結します。 必要最低限の人数で作業を回せるので、人件費のコスト削減にもつながります。
倉庫作業の業務改善にはシステム導入がベスト
倉庫作業の業務改善を行うにあたって、先に挙げた内容すべてを現場の手作業だけで行うのは時間もかかり、そのための人員が必要となります。
そこで、あらゆるムダを省くという点から考えて、システムの導入が最適といえます。
次から、倉庫作業の業務改善に対するシステム導入のメリットや、その継続性についてもみていきましょう。
倉庫作業にシステムを導入するメリット
倉庫作業のシステムには、代表的なものにQRコードやバーコードを読み取って在庫やロケーションを管理するシステムがあります。 入荷した製品のバーコードと、それをしまう棚のバーコードを読み取ると、どこに何がどれだけあるのかを自動でデータ化が可能です。
こういったシステムに、工場や倉庫内だけでなく、オフィスのパソコンからもアクセスできるようになれば、だれもが一目瞭然で進捗も管理可能となります。
さらに、作業者の位置情報から台車などのツールの空き具合、最適な運搬ルートまでを一括管理できるシステムは、倉庫作業の業務改善として大きな効率化を図れます。 人が手作業で管理するのは限界もあり、システム導入には人為的ミスを減らす効果も見込めます。
継続した改善にはシステム導入が適切
倉庫の状況が日々変化していく中で、人の手だけでは継続した業務改善が難しいケースもあります。 倉庫作業は止まることはありませんので、継続した仕組みづくりを人の手だけで完結するのは至難といえます。
そこで、業務改善のシステムを導入すれば、あらゆる仕組みが自動化できて、作業の効率化・人為的なミスの防止・人件費の抑制など、さまざまな効果とその継続が期待できます。
また、システム導入で業務改善を行えば、管理監督者の負担も減り、作業者も仕事がやりやすくなります。 倉庫作業の業務改善を継続するのにもシステム導入はメリットがあるといえるでしょう。
まとめ:倉庫作業の業務改善で効率化を図ろう!
倉庫作業には、物の動きとその管理、作業における人為的な要素など、さまざまな問題が絡み合っているため、すべてを改善していくこととそれらを継続していくことは非常に難しい課題です。
作業効率化のために、まずは現状抱えているムダをひとつひとつ把握し、そのうえで業務改善システムの導入を検討することが効果的です。 自社工場に最適なシステムを活用することで、倉庫全体の生産性向上を目指しましょう。
お電話でのお問い合わせ
【東京】03-3257-1141
【大阪】06-6442-1329
受付時間:
平日9:00 - 17:00
(土日祝日、年末年始を除く)