コラム
Column
2022.10.14
工場のレイアウトを最適化するために動線分析が必須なワケ
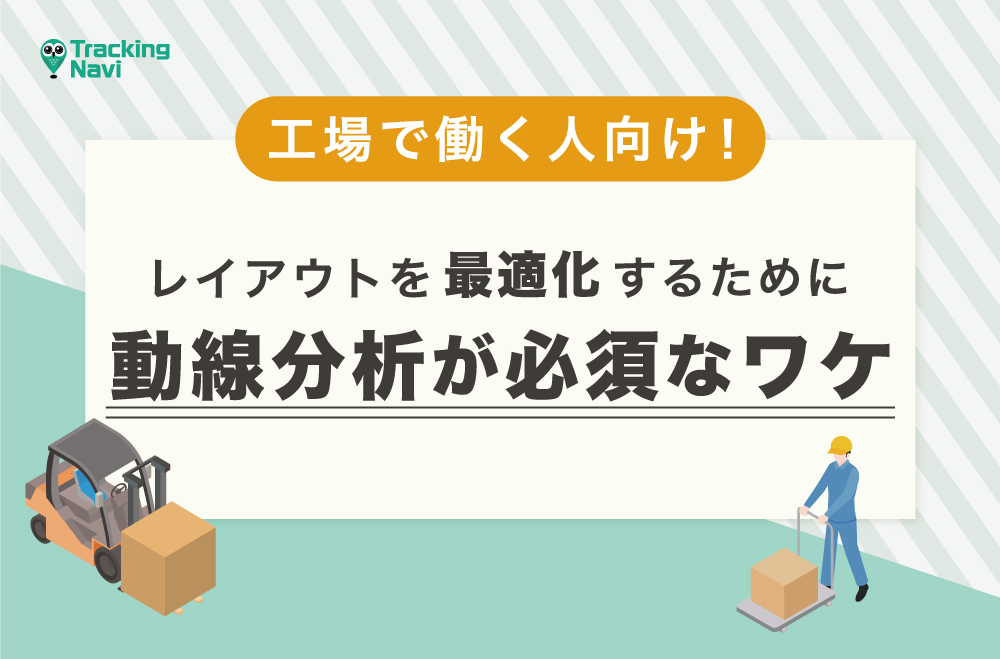
工場のレイアウトを最適化することは、業務効率の向上につながることはもちろんのこと、安全性の確保にもつながります。
もし工場のレイアウトが最適化されていない状態で業務に取り組んだ場合、人の動きが重なり業務効率が落ちたり、接触事故の原因になったりしてしまうため注意が必要です。
本記事では、工場のレイアウト最適化に向け、動線分析を行うべき理由を解説します。
工場のレイアウトでお悩みの方は、ぜひ本記事を参考にしてください。
目次
工場の動線を改善すると得られる効果
工場のレイアウトを最適化する上で、作業者の動線を分析することは欠かせない作業工程のうちの1つです。
動線分析を行うことで工場内の作業者の流れを把握できるため、現状の工場レイアウトに対する問題点を洗い出すことが可能です。
工場の動線を改善することで得られる効果は、大きく分けて以下の3つがあります。
・動線(移動距離)の短縮
・業務効率の向上
・安全性の確保
それでは、それぞれの効果について詳しく見ていきましょう。
動線(移動距離)の短縮
動線分析を行うことで、業務中に発生している移動のムダを発見でき、動線を短縮することが可能です。
動線分析を行う場合、まず初めに現状の動線の長さを算出しておきましょう。動線分析後に改善したレイアウトでの動線と現状の動線の長さを比較することにより、どれだけ動線が短縮できたのかが定量化できます。
動線の改善により、短縮できる移動距離は短いものかもしれません。しかし、そのわずかな移動距離の改善が積み重なることにより、長期間で考えた時に大きな改善につながります。
動線が短縮されることで移動にかかる時間が短縮され、その結果、別作業に費やせる時間を増やすことができます。動線を短縮するためには、以下の点に注目して動線分析を行うと良いでしょう。
・頻繁に使う設備や棚への移動の動線が長くなっていないか
・作業者や搬送車の流れが入り組んでいて、動線が錯綜していないか
・何度も往復している距離を短くできないか、往復する回数を減らせないか
動線を分析することで、予想以上に長い距離を移動していることがわかります。
往復回数が多い動線や1回当たりの移動距離が長い箇所を改善していきましょう。
業務効率の向上
動線分析では動線を短縮できるだけでなく、業務の流れも見直すことができるため、業務効率の向上にもつながります。
下記の点に着目することで、改善へと繋げることが可能です。
・工程に適した設備配置が行われているか
・同じ工程なのに作業者によって動線が著しく異なっていないか
・本来その工程で行く必要がないはずの、予想外の場所への移動が発生していないか
・長期間、誰も行かないエリアがないか(不要なものの保管にスペースを使っている可能性がある)
動線分析により現状の業務の流れにムダがないかを見直した上で、最適なレイアウトを考えましょう。
安全性の確保
工場内では不適切なレイアウトが原因で人が密集してしまい、事故やトラブルを引き起こしてしまう可能性もあります。
事故やトラブルが発生する直前の状況も含めて、リスクの確認と回避をしていかなければなりません。
動線分析を行う際には、以下に着目して分析を行うことにより、安全性も確保できます。
・動線が錯綜している場所について、接触事故が発生しやすくなっていないか
・作業者が滞留している場所について、エリアや通路が狭すぎないか
・伝達が多い部署同士が離れすぎていないか
接触事故が発生しやすい場所や滞留が発生している場所は、動線を改善することにより、事故を未然に防ぐことができます。
また、伝達が多い部署同士の距離が離れていると、伝達ミスによるトラブル発生の原因になってしまいます。
動線分析を行なった際に、伝達が多い部署同士の距離を確認し、距離が離れているようであれば部署間の配置も改善するようにしましょう。
工場の動線分析を行うための手法
工場の動線分析を行うための手法はさまざまです。
下記に工場の動線分析を行うための代表的な手法とその特徴をまとめました。
手法 | 特長 |
---|---|
超広帯域無線通信(UWB) | 数GHzの広い周波数帯域を使用し障害物による影響が少ない点が特徴です。 30m~50mの間隔でUWBの固定機を工場の上部に設置することで位置情報が取得できます。 |
自律型行動計測システム(PDR) | 加速度・ジャイロ・磁気などのセンサーを使用し、作業者の移動方向と移動量を推定できます。 これらのセンサーはスマホにも搭載されているため、個人が所有するデバイスをそのまま計測システムに利用できる点が特徴です。 |
Bluetooth Low Energy(BLE) | 低消費電力でBluetoothの信号を発信するビーコンを使用します。 工場内でビーコンを10m~50mの間隔で設置することで、ビーコンからの信号で位置情報の推定を行うことが可能です。 |
工場の動線分析を行う上での難点
工場の動線分析は、動線の短縮や業務効率の向上、安全性の確保といった多くのメリットがありますが、動線分析を行う際に注意しなければならない点もあります。
<工場の動線分析を行う上での難点>
・業務を行いながら動線分析を行う必要がある
・動線分析を行う際にコストがかかってしまう
業務を行いながら動線分析を行う必要がある
動線分析を行うときは、現状の動線の問題点を洗い出す必要があるため、当然ながら業務を行いながら動線分析を行う必要があります。
業務と並行して動線分析を行わなければ、精度の高い分析結果を得られずレイアウトの最適化にもつながりません。そのため、動線分析の手法として通常業務に支障をきたさない手法で分析を行う必要があります。
動線分析を行う際にコストがかかってしまう
上記で解説した動線分析の手法の中には、多額のコストがかかってしまう手法もあります。
例えば、超広帯域無線通信(UWB)を利用した動線分析の場合、工場内にUWBのセンサーを設置しなければなりません。
工場が大きい場合、多くのUWBセンサーが必要になり、設置するために多額の費用がかかってしまいます。 このように動線分析では、多額のコストがかかってしまう手法もあるため、動線分析によるレイアウト最適化後に充分なリターンを得られるかを検討する必要があります。
工場の動線を分析できたらレイアウトの最適化へ
工場の動線分析が完了したらいよいよレイアウトの最適化を行いましょう。
レイアウトの最適化は以下の手順で行います。
1.動線分析
工場内の人やものの流れを把握します。
現状の動線の長さも算出し、レイアウト改善後の効果を定量化します。
2.物量分析
動線を改善するときに優先する重点商品を決定するため、全体の物量を把握します。
販売量・入出荷件数などを参考に、重点管理対象となる商品を決めます。
3.類似工程分析
人やものが移動する初工程から最終工程を把握し、業務工程が似ているグループは近くに配置します。
4.レイアウト相関分析
物量や工程順、作業員の能力などの要素から、設備や工程の近接性の評価をします。
5.レイアウト設計
手順1~4を参考に設備・工程の配置を決定し、レイアウトの設計を行います。
6.動線・レイアウト改善実施
手順5で設計したレイアウト案を基づきレイアウトの変更を行います。
7.進捗管理と検証・定着化
レイアウト改善の進捗状況を把握します。
レイアウト改善によって問題点が改善されているかも検証します。
まとめ:工場のレイアウトを最適化するために動線分析が必須なワケ
本記事では工場のレイアウトを最適化するために必須である動線分析について解説しました。
動線分析では現状の問題点を洗い出すことができ、業務効率の向上や安全性の確保などの効果があります。
動線分析にはさまざまな手法があるため、工場のレイアウトを最適化したい方はぜひ本記事を参考にし、動線分析を行なってみてはいかがでしょうか。
お電話でのお問い合わせ
【東京】03-3257-1141
【大阪】06-6442-1329
受付時間:
平日9:00 - 17:00
(土日祝日、年末年始を除く)